The Wool Wire | June 26, 2024
Putting pellets to the test, saving Swedish wool, dyeing without water, plush new Merino seats for the wool jet, saying hello to a shearing family and goodbye to Zeilingers
News snippets from the wool world
Hello, my friends!
Welcome back to another exciting episode of As the Wool Turns. We have action. We have excitement. We have drama and adventure. We even have an update on the wooljet!
🐑 First, a quick heads-up to members of the Foundation Flock: A juicy new quiz is headed to your inboxes tomorrow. Since it's summer reading season, this one is all about literary sheep and shepherds. Also, our next Flock Talk is this Sunday, June 30th at 7pm EDT. You'll get the magic link beforehand. (If you're not yet a member of the Foundation Flock, you're more than welcome to join us.) 🐑
Pellet Poetry
You've heard me wax poetic about wool pellets again and again. And I'll probably keep doing so, because they represent such a huge shift in how we can value our wool and care for our soil.
But it's always important to balance those lofty claims with science-backed data on what wool actually does to soil. The women behind EcoWool Canada have partnered with Ontario's Brock University to get at the facts. They're growing spinach, sweet peppers, marigolds, basil, and yellow beans in pots containing pellets, conventional fertilizers, or no soil amendments at all.
Every activity is being recorded during the experiment, such as how much water is added, and plants are monitored and weighed at the end.
After harvesting the crops, the researchers will use sophisticated instruments at the Brock-Niagara Validation, Prototyping and Manufacturing Institute (VPMI) to measure organic carbon and nitrogen quantity and quality of soil and water samples.
I'll definitely keep following this one.

Putting the "oooh!" in CO2 dyeing
We know that dyeing can be a water hog. Conventional textile dyeing uses anywhere from 25 to 40 gallons of water to dye just two pounds of fabric, depending on the fiber, fabric, color, and dye technique. Meanwhile, dye and other textile treatments are responsible for some 20% of all industrial water pollution globally.
Clearly, something needs to change. The Dutch company DyeCoo has invented a waterless closed-loop dye system that uses carbon dioxide as a solvent. Yes, DyeCoo machines cost more than conventional dye systems. But just one machine can process up to 800 tons of polyester a year, saving 32 million liters of water, avoiding the use of 160 tons of chemicals, and completely eliminating the release of wastewater into our environment.
The key word here is "polyester." DyeCoo says its process is only suitable for synthetic PET fabrics and yarn. However, a new study explores the potential effectiveness of "using supercritical CO2 as a non-aqueous dyeing medium" to dye wool.
The results showed that K/S values up to 5.5 under the optimal dyeing condition of 383.15 K, 23 MPa, and 70 min were obtained, indicating shorter reaction time and higher K/S values compared to similar studies.
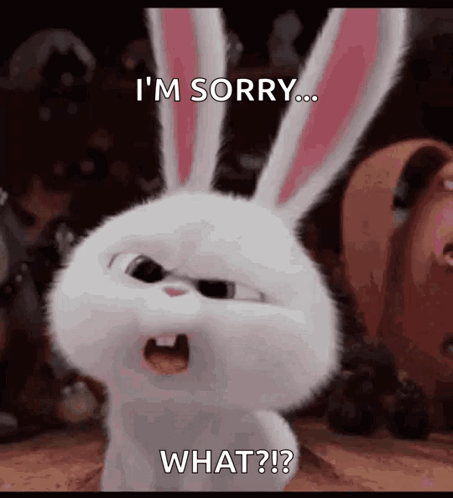
Maybe you understood that better than I did. But the bottom line is that the initial results are promising enough to merit further exploration. Slow but steady, we'll get there.
Sweden discovers the merits of combing
Still on the subject of waste, the Swedish Wool Initiative is making exciting progress in reducing waste and adding value to its wool. At issue was the high amount of vegetable matter present in Swedish wool, the result, they maintain, of the country's top-tier animal welfare practices. However, this meant that much of the wool was unsellable.
However, by adding the simple step of combing the wool, they've been able to remove the plant matter and create a "soft and pliable worsted yarn." Combing usually generates a high amount of waste itself, but presumably not enough waste to offset the value combing adds to the remaining wool.
According to Gösta Magnusson, chairman of Klippan Yllefabrik, "Swedish wool has traditionally been relegated to coarser materials and stuffing. This new worsted yarn, however, offers something entirely different - a fine yarn from Swedish wool, crafted in Europe, ideal for sustainable fashion. It's slightly thinner and perfect for knitting warm sweaters."
Already, the Swedish Wool Initiative is producing tangible results for their local wool industry. Surely we can do something similar in other countries too?
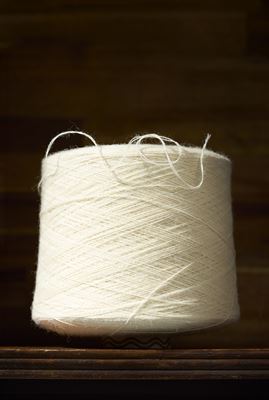
Keeping it in the family
Wisconsin has never been considered a major wool producer. Since 1997, wool production in the state has declined by 45%—primarily because demand for this wool continues to evaporate in favor of synthetics. But the state is still home to some 78,000 sheep who need shearing every year as part of their ongoing care.
I absolutely loved this Wisconsin Public Radio profile of a Wisconsin sheep shearing family. It's a wonderful introduction to the trade, encompassing the physical challenges, logistics of the shearing shed, and fine craftsmanship of doing a good job.
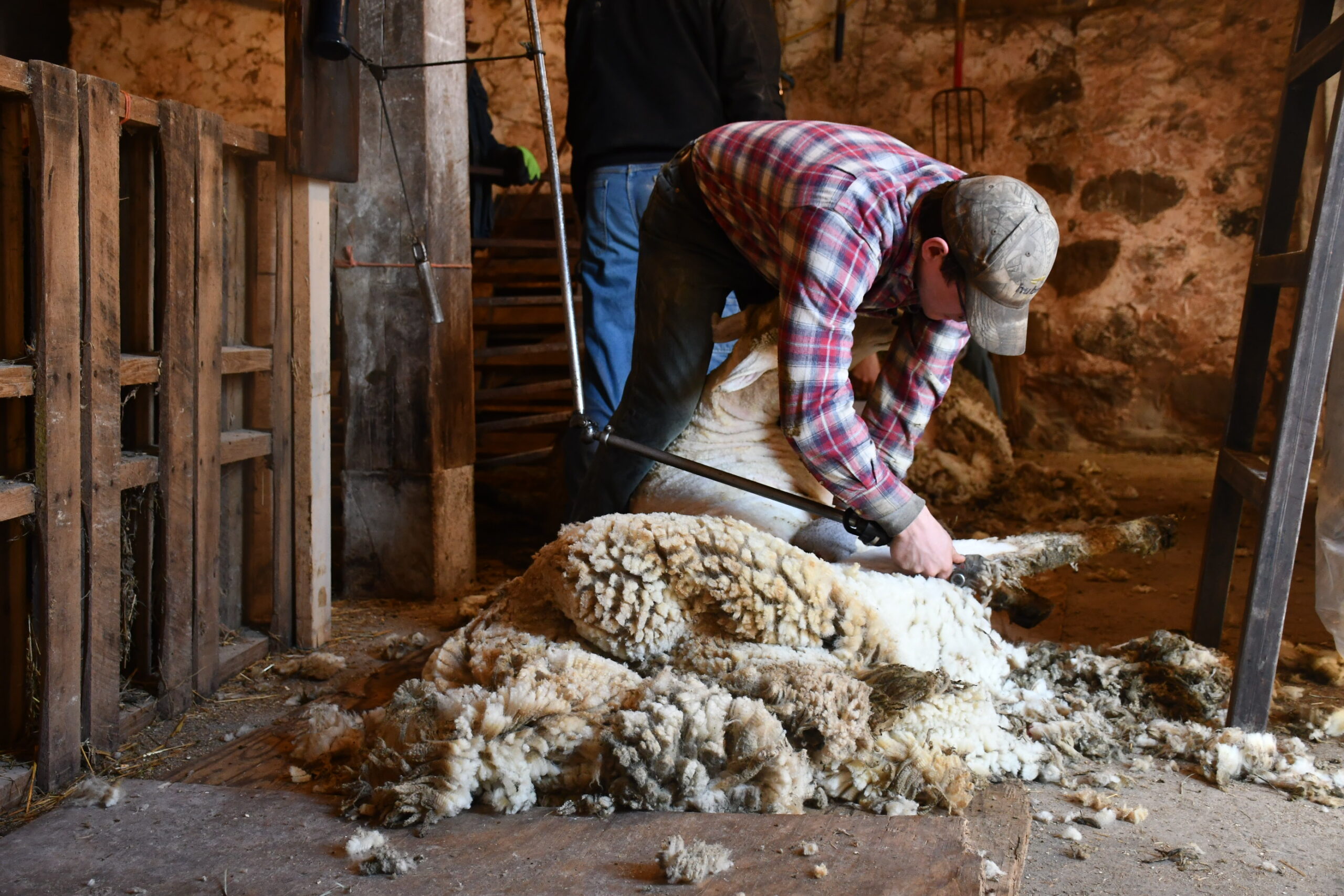
Goodbye to Zeilinger
And speaking of family businesses, for almost 115 years, the Zeilinger family, and Zeilinger Wool Company, have been a fixture of the American wool landscape. Countless small farms and yarn companies—and even hobby fleece collectors such as myself—have relied on Zeilinger for scouring, processing, and spinning.
Alas, our landscape is changing. Earlier this week, the company announced that it was no longer operating as a fiber processor. As hard as this news has been, I take comfort in knowing that Jon Zeilinger will carry on the family trade as Sales Engineer for Crescent Woolen Mills, which will also finish processing all existing Zeilinger orders.
My gratitude and best wishes to the entire Zeilinger family.
On that note, I'll let you go.
Thanks, as always, for your readership and your support!
Until next time,
Clara